Československo bolo kedysi obuvníckou veľmocou. Túto oblasť preslávil hlavne Tomáš Baťa, pričom asi najznámejšou slovenskou obuvníckou fabrikou bol v tom čase národný podnik ZDA Partizánske. Obuvnícky priemysel výrazne napredoval a z obuvi sa stal výnosný vývozný artikel. V tejto fabrike pôvodne pracoval aj Ivan Arvay, zakladateľ firmy Artra, ktorá sa špecializuje na výrobu pracovnej obuvi.
Ako spomína, ZDA Partizánske bolo obrovská fabrika približne so 16-tisíc zamestnancami, ktorá ročne vyrábala viac ako 30 miliónov párov obuvi. „Všetci v Partizánskom vedeli vyrábať obuv,“ spomína I. Arvay. Vo fabrike pracovala aj jeho mama, ktorá bola majsterkou v jednej z mnohých šijacích dielní, kde sa zhodou okolností vyrábala pracovnú obuv.
„Po vyštudovaní Obchodnej fakulty Vysokej školy ekonomickej v Bratislave som začal vo fabrike pracovať ako vedúci odbytu strojov a polotovarov, kde som bol približne šesť rokov. Po revolúcii sa však fabrika ZDA Partizánske začala rozpredávať a jej pozícia spolu s výrobou začali rapídne klesať. Tak bolo potrebné zmeniť výrobný program. Matne si spomínam, že sa uvažovalo o vyrobe zliatinových kolies pre lyžiarske vleky do Rakúska či nízkozdvižných antikorových vozíkov pre potravinársky priemysel do Švajčiarska,“ hovorí I. Arvay.
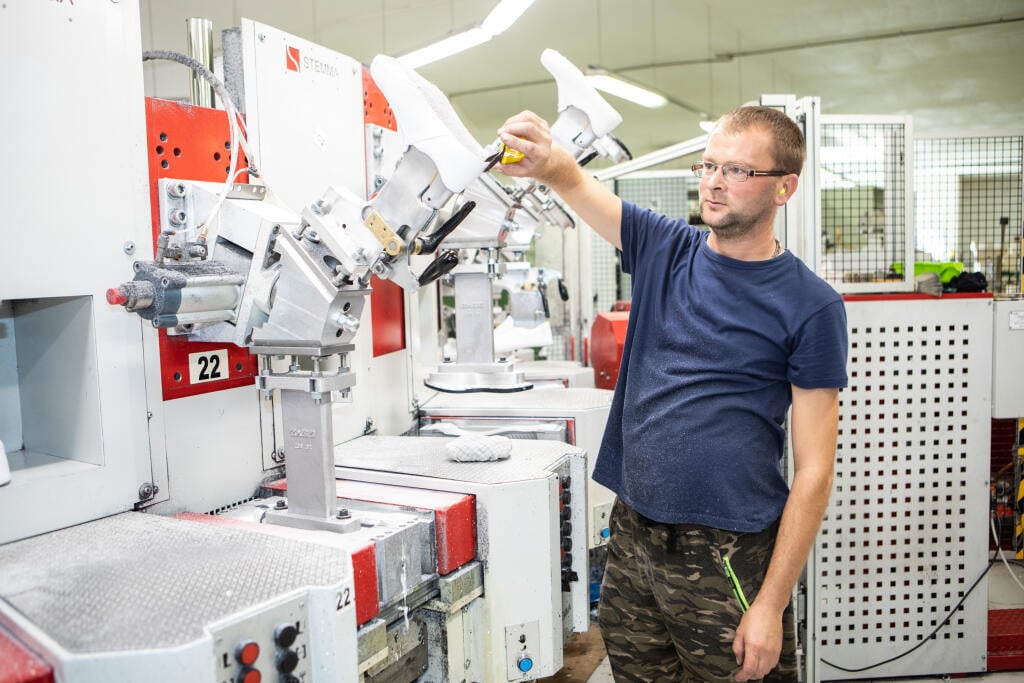
V tom čase však už nevidel svoju budúcnosť spojenú s fabrikou, a tak si zo dňa na deň povedal, že končí. Keďže bol ženatý a s manželkou mali dve malé deti, museli rýchlo uvažovať, čo ďalej. Do kariet im zahralo to, že v tom čase končil monopol národného podniku Rempo, cez ktorý sa v čase socializmu predávali ochranné pomôcky.
Na začiatku pomohla mama
Začiatkom 90. rokov I. Arvay najskôr obuv len predával ako fyzická osoba. Názov Artra vznikol spojením jeho mena a anglického slova trade, teda obchod. Názov je navyše palindróm – slovo, ktoré rovnako znie aj odzadu. V novembri 1993 vznikla súčasná firma s tromi spoločníkmi, ktorí však postupne odišli. „Od januára 1998 som zostal vo firme sám s manželkou. V začiatkoch sme vyrábali približne 50 až 70 párov obuvi denne a zamestnávali sme okolo 30 ľudí,“ spomína I. Arvay.
Postupne sa kapacita výroby zvyšovala a spolu s ňou počet zamestnancov. „V začiatkoch boli podmienky na podnikanie, paradoxne, veľmi dobré. Keď to poviem obrazne, v pondelok sme kúpili materiál, v utorok sme vyrobili a v stredu sme predali a dostali peniaze v hotovosti. Vo štvrtok sme kúpili ďalší materiál a celý cyklus sa opakoval. Prakticky neexistovali nijaké splatnosti faktúr a cash-flow bol veľmi rýchly.“
V začiatkoch mu pri podnikaní výrazne pomohla jeho mama, ktorá presne vedela, aké sú operácie pri výrobe pracovnej obuvi, ako naplánovať výkonnostné normy. Syn sa, naopak, vedel pohybovať v ekonomických a obchodných záležitostiach.
V hlavnej úlohe polyuretán
Pri výrobe obuvi existuje viacero technológií. Arvayovci začali s výrobou lepenej obuvi. Prelomovým obdobím vo výrobe bol rok 2003, keď kúpili prvú osemnásťstanicovú linku s technológiou priameho vstreku dvojhustotného tekutého polyuretánu do uzatvorených podošvových foriem a ich obuv už bola schopná konkurovať tej zo západnej Európy. „Prvú linku sme kupovali staršiu, repasovanú, pretože s podnikaním sme začínali od nuly. Na začiatku som mal len tisíc korún, napriek tomu sme všetko financovali zo zarobených peňazí a nikdy sme nevyužili peniaze od investorov,“ hovorí I. Arvay a dodáva, že sa stretol aj so záujmom o kúpu ich spoločnosti, hlavne zo zahraničia.
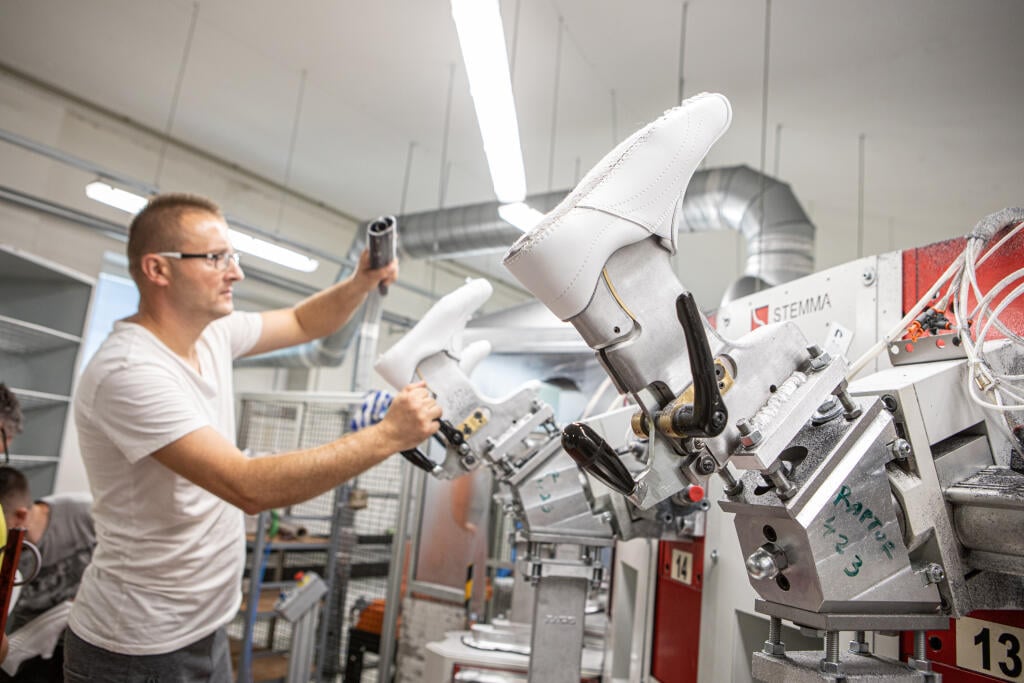
Ako ďalej vysvetľuje, podošvová zmes je polyuretán, ktorý je v tekutom stave. Ten sa pri tejto technológii vstrekuje do dutiny, ktorá sa vytvára formou a stielkou kopyta. Dnes sa už takmer 95 percent pracovnej obuvi vyrába z polyuretánu. Hlavnou výhodou je predovšetkým nízka odernosť a nastaviteľná relatívna hustota materiálu. Pracovná a bezpečnostná obuv má pritom svoje normy a certifikáty, ktoré platia pre celú EÚ.
V roku 2007 kúpila Artra druhú 18-stanicovú linku. Zvyšovala sa výroba a modely, ktoré vyrábali, boli čoraz konkurencieschopnejšie, čo sa prejavovalo aj v predaji. Arvayovci najskôr predávali svoju obuv na Slovensku a niečo málo vyvážali do Česka. Neskôr sa vývoz rozrástol do ďalších krajín ako Poľsko, Maďarsko či Rumunsko.
Dnes je Artra orientovaná proexportne a približne 72 percent obuvi vyváža do 27 štátov Európskej únie. „Pokúšali sme sa vyvážať aj do USA alebo do krajín mimo EÚ, no tam platia iné certifikácie, ktoré nie sú lacné. Povedali sme si, že nám európsky trh stačí,“ skromne dodáva I. Arvay. V súčasnosti je podľa neho možné povedať, že firma Artra je v oblasti výroby pracovnej obuvi jednou z najväčších v strednej Európe. Za minulý rok dosiahla tržby viac ako 11,5 milióna eur a jej zisk bol viac ako 1,5 milióna eur.
Pokus s vlastnou predajňou
Artra nemá dvoch či troch veľkých klientov. Obuv od nej kupujú stovky malých a niekoľko väčších zákazníkov. „Ak máte dvoch zákazníkov a stratíte jedného, 50 percent obratu je preč. Ak ich máte tisíc a prídete o dvadsiatich, stratíte len dve percentá.“ Medzi najväčších zákazníkov patria napríklad spoločnosti Kaufland, Lidl či Jaguar Land Rover.
Pri špecifickom sortimente, akým je pracovná obuv, moderný marketing v podobe sociálnych sietí nedáva zmysel. Pracovnú obuv si väčšinou nekupuje jednotlivec, ale nákupca určitej firmy, ktorá ich dáva zamestnancom. Pre Artru je preto hlavným marketingovým nástrojom dobré meno, kvalitná obuv, servis a katalóg výrobkov. Začiatkom roku 2009 si vo firme mysleli, že bude dobré, ak si zriadia vlastnú kamennú predajňu pre živnostníkov, ktorí zamestnávajú zopár pracovníkov. V Bratislave si preto prenajali priestory, ktoré potom fungovali približne šesť rokov. Predajňu nakoniec museli zavrieť, pretože vzhľadom na prevádzkové náklady bolo jej fungovanie nerentabilné.
Ďalšie prelomové obdobie nastalo v roku 2015, keď firma kúpila najnovšiu 24-stanicovú linku na technológiu priameho nástreku. V tomto prípade však išlo celkovo o druhú linku na svete a vôbec prvú v Európe, pretože linka používala iný spôsob než tie predchádzajúce. Tie tekutý polyuretán vstrekovali. Najnovšia linka materiál do dutiny sprejuje. „Má to rôzne výhody, pričom tento spôsob sa dá použiť aj na rôzne typy športovej obuvi.“
Kvalita za vyššiu cenu
Dnes má Artra svoje meno aj vďaka tomu, že sa nikdy nesnažila byť najlacnejšia a v oblasti pracovnej obuvi o nej vedia výrazne väčší výrobcovia. „Nikdy sme nechceli konkurovať čínskym výrobkom. Koncom roku 2008 sme si dali v Číne naceniť výrobu niekoľkých modelov podľa svojho zadania. Cenová ponuka bola nakoniec približne rovnaká. Ani rovnako ako my nemajú usne a musia ich kupovať. Rozdiel je len v cene práce, ktorá je u nich o niečo nižšia. Ak vidíte obuv, ktorá stojí dvanásť eur, nekupujte ju. Takáto topánka nemôže byť dobrá,“ hovorí I. Arvay a dodáva, že v Artre stavili na kvalitu a komfort za vyššiu cenu.
V Artre veria, že keď zamestnancom vytvoria dobré pracovné podmienky, tí sa za to odmenia kvalitnými výrobkami. V súčasnosti vo firme pracuje 200 vlastných a 30 externých zamestnancov. Do fabriky v Partizánskom chodieva zakladateľ každý deň, pretože na jednom mieste sa nachádza celá výroba, sklad materiálov a sklad hotových výrobkov. Viacero zamestnancov pozná osobne a po chvíli zamyslenia hovorí, že si tyká asi s päťdesiatimi až sedemdesiatimi pracovníkmi. Jediným miestom oddeleným od výrobného areálu je administratívna časť, ktorá je vzdialená zopár kilometrov od Partizánskeho, v Oslanoch. Víziou však je spojiť ju so zvyškom firmy.
Zareagovali na koronakrízu
Vlani firma vyrobila viac ako 520-tisíc párov pracovnej obuvi. Pandémia nového koronavírusu ju príliš nezasiahla, no určitý pokles dopytu zaznamenala. Na jar začala šiť rúška, pričom výroba obuvi naďalej pokračovala, no v menšom objeme. „V priebehu pár dní sme z dôvodu nedostatku rúšok veľmi rýchlo zareagovali a začali sme ich šiť. Dopyt po nich bol extrémny. Rúška sme predávali hlavne fabrikám, ale aj obchodníkom, ktorí predávajú našu obuv nielen na Slovensku, ale aj v zahraničí.“ Vo výrobni sa počas šitia rúšok prakticky nezatvorili dvere ani sa nezhasínalo. Pracovalo sa 24 hodín denne a za dva mesiace vyrobili viac ako 800-tisíc rúšok. Výroba a predaj v tom čase nedostatkového sortimentu napokon firme pomohli preklenúť slabšie obdobie. Práce bolo síce menej, no firma sa už dostáva do pôvodného tempa. Dnes sa kapacita výroby obuvi vrátila na úroveň spred krízy, pričom I. Arvay si myslí, že tohtoročné výsledky by mohli byť ešte lepšie než tie vlaňajšie. Denne dokáže Artra vyrobiť asi 2 400 párov obuvi.
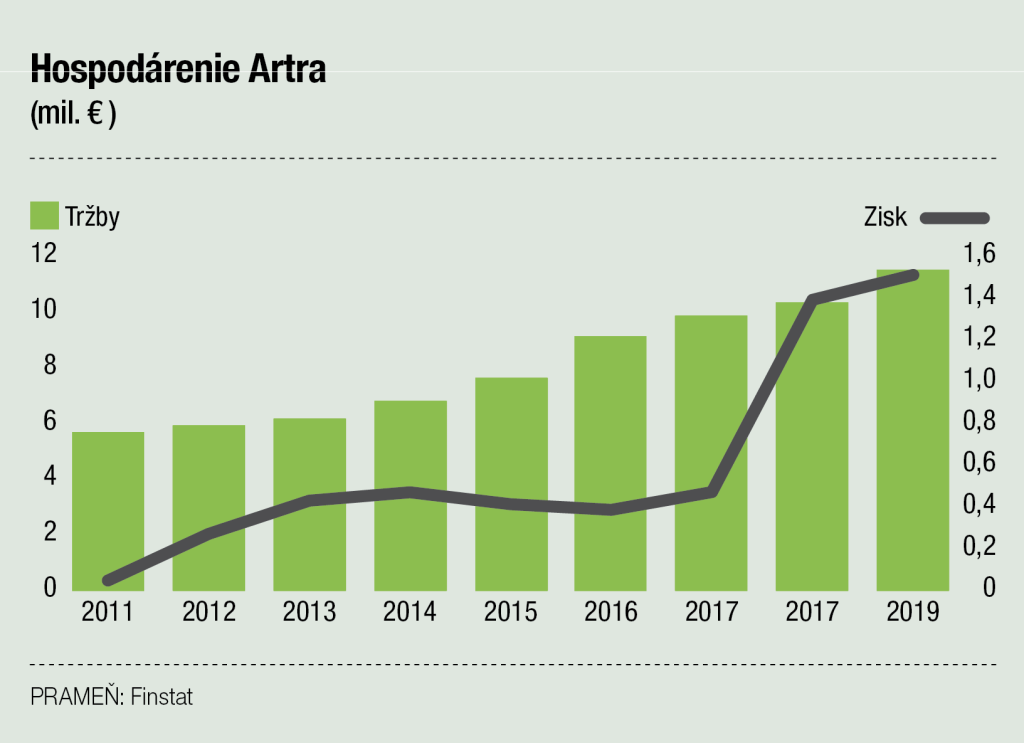
Zamestnanci pracujú v jednej, respektíve dvoch zmenách. V prípade potreby je možnosť pracovať aj na nočnej zmene, no tento koncept sa im príliš neosvedčil. „Pre človeka nie je štandardné preorientovať sa tak, aby vedel kvalitne robiť aj v noci. Výrobky, ktoré boli vyrobené v noci, boli síce dobré, no percento reklamácií bolo o niečo vyššie v porovnaní s tými, ktoré boli vyrobené počas normálnej zmeny.“
Dvaja synovia a manželka
Asi najviac postihla firmu kríza v roku 2009, keď musela v priebehu niekoľkých mesiacov pre prudký pokles objednávok prepustiť niekoľkých zamestnancov. Vtedy v nej pracovalo viacero ľudí, ktorí boli vo firme od začiatku. Bez nepopulárnych opatrení by firma situáciu nebola zvládla, podľa I. Arvaya to bolo kritické hlavne z emocionálnej stránky.
Vo firme pracujú okrem manželky aj dvaja zakladateľovi synovia. Manželka Alena sa venuje hlavne back officeu. Synovia majú za sebou aj štúdiá v zahraničí, čo im prinieslo jazykovú zdatnosť a možnosť vidieť procesy a trendy vo svete. Starší syn Martin je riaditeľ obchodného úseku a mladší Ivan pracuje ako manažér marketingu a nákupu materiálu. „Ja som ich do práce v našej firme, pochopiteľne, nenútil. V podstate som ich hodil do rieky, aby sa naučili plávať, s tým, že im pomôžem. Dnes sú z nich celkom dobrí plavci.“ Za svoje tretie dieťa považuje samotnú fabriku.
Do budúcnosti si želá, aby aj ďalšia generácia firmu zveľaďovala. „Keď človeka práca baví a je v nej dobrý, vidieť to aj na výsledkoch. Rád sa obklopujem ľuďmi, ktorí sú lepší ako ja. Ešte na začiatku som hovoril, že máme len dve možnosti: buď budeme najlepší, alebo prví. Iné možnosti nie sú a naozaj sa to ukazuje ako správne rozhodnutie.“
Ambiciózne plány
Množstvo odvetví sa časom výrazne mení, pričom obuvnícke remeslo nie je výnimkou. Technológie sa posúvajú vpred a z ľudí sa v určitom slova zmysle stávajú aj programátori. Dnes to už nie je klasická lepená obuvnícka výroba s kladivkom a klinčekmi. Je to automatizovanejšie a dokáže sa to naučiť takmer ktokoľvek. Obuvnícke zručnosti už nie sú až také potrebné ako kedysi. Ľudia musia vedieť obsluhovať stroje, naprogramovať ich a v prípade potreby opraviť.
„Jedna zahraničná firma na výrobu obuvníckych strojov pred časom predstavila svoju víziu výroby obuvi o 30 až 50 rokov, s ktorou sa nestotožňujem. Jej vízia predstavovala v podstate kiosk alebo automat, do ktorého sa vloží noha. Ten ju naskenuje a počas toho, ako si človek nakúpi alebo pôjde do reštaurácie, bude topánka v priebehu troch hodín vyrobená. Ja si nemyslím, že to takto bude fungovať. Nedokážem si predstaviť, že pri bežnej obuvi je možné nahradiť ručnú výrobu,“ tvrdí I. Arvay. Čo sa týka budúcnosti, v Artre sa tešia na novú formu podošvy, ktorá je ladená do športového charakteru a bude predstavená začiatkom nasledujúceho roka.
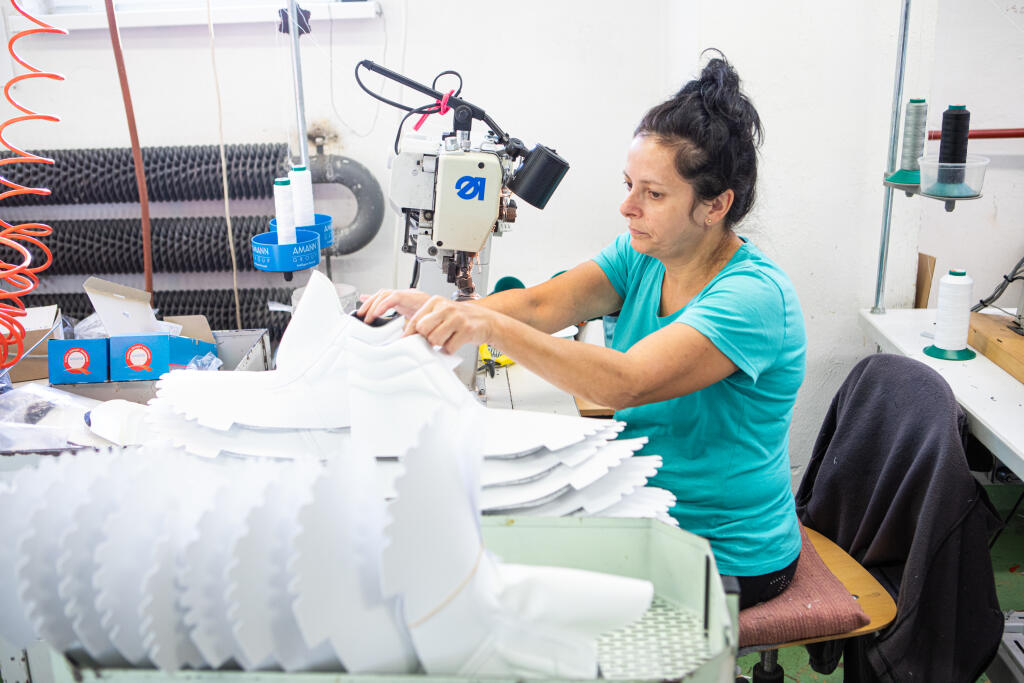
Vo firme sa zároveň snažia staviť na efektivitu. Odchádzajú od komplikovaných vzorov, ktorých výroba vyžaduje veľa času. „Nechcem hovoriť za synov, no moja predstava je, aby sme boli schopní o päť alebo desať rokov vyrábať okolo milióna párov pracovnej obuvi ročne.“
Obstaranie obuvníckych strojov pritom vôbec nie je lacná záležitosť. V princípe sa dá povedať, že jeden stroj stojí okolo milióna eur a každá z podošvových foriem od 4 000 do 6 000 eur. Bez foriem nie je možné vyrábať a dokupujú sa samostatne. Celkovo je potrebných asi 25 foriem, takže na kúpu kompletného stroja treba približne 1,2 milióna eur. Pri výrobe používajú aj dva až tri roboty, ktoré separujú formy a driasajú zvršky. Roboty stoja v závislosti od druhu od 50- do 80-tisíc eur, čiže jedna kompletná linka vyjde na 1,5 milióna eur.
„S výrobou topánok v Partizánskom začal Baťa a ten mal veľmi dobre prepracované niektoré riadiace procesy. Dodnes niečo využívame pretransformované na naše podmienky. Mnohé myšlienky, ktoré mal, ako napríklad venuj sa poctivej a úprimnej produkcii, peniaze sa ti nevyhnú, inými slovami nerozmýšľaj o tom, koľko na nej zarobíš, rob dobrú topánku, vyrob kvalitne a uvidíš, ako to predáš, boli úžasné a my sa ich snažíme držať. Možno aj vďaka tomu sa nám darí robiť kvalitne to, čo robíme,“ uzatvára I. Arvay.