Práčka, umývačka riadu, chladnička či digestor sú pevnou súčasťou bytu a významne ovplyvňujú atmosféru domova. Aj preto hrá úroveň hluku a vibrácií stále väčšiu úlohu pri výbere domácich spotrebičov. „Význam tohto parametru rastie z roka na rok. Dokonca je to kritériom, ktoré môže stopnúť sériovú výrobu niektorého z produktov“, hovorí Otto Petraška, vedúci košického oddelenia Vibrácie a akustika v spoločnosti BSH.
Výskumná skupina vznikla v roku 2004. V tom čase mala troch ľudí, dnes tu pracuje šestnásť expertov a na nedostatok práce sa nemôžu sťažovať – okrem „domáceho“ závodu BSH v Michalovciach poskytujú služby ďalším ôsmim divíziám koncernu Robert Bosch. Podieľajú sa na optimalizácii hlukových a vibračných parametrov prakticky celého výrobného sortimentu, od záhradných nástrojov ako sú napríklad krovinorezy až po elektromotory do hybridných automobilov.
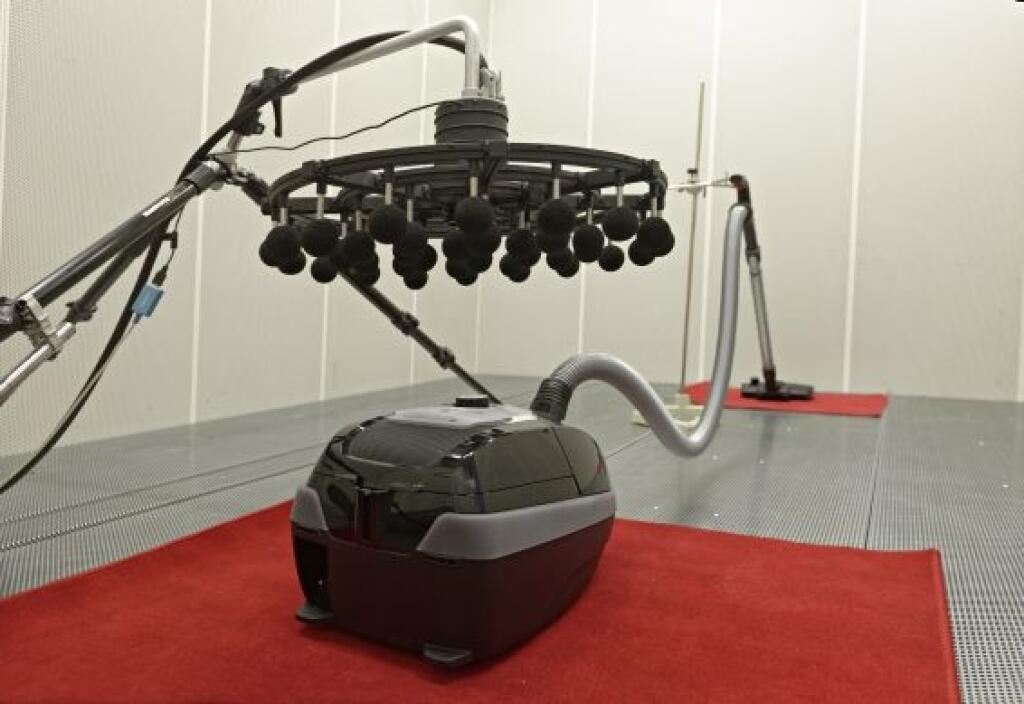
In´genius ProSilence 59 drží rekord najtichšieho vysávača na trhu a je pýchou košického laboratória zvukového dizajnu.
Zvukový dizajn
Je jasné, že pračky či umývačky riadu prémiovej značky Bosch nesmú zniesť „lacno“ a musia plniť očakávania zákazníkov. Na dosiahnutie tohto cieľa využíva košické centrum paletu nástrojov psychoakustiky. „Robíme testy so skupinami ľudí, ktorým prehrávame vzorky zvukov. Na základe ich hodnotenia stanovíme cieľ akustiky, aby splnila očakávania zákazníkov. Zároveň zohľadňujeme požiadavku nášho marketingu, aby bol zvuk ,powerfull´, teda mal silu, ale zároveň nebol ,rušivý“, vysvetľuje O. Petraška.
„Potvrdzuje sa nám, že zákazníci uprednostňujú ,očakávané zvuky´. Pračka má znieť ako čľapkanie vody, digestor evokovať vietor a kávovar žblnkot kávy“, vysvetľuje senior špecialista centra pre akustiku a vibrácie Rastislav Andrejco.
Košické laboratórium pre zvukový dizajn, tzv. sound design, využíva na výskum zvukových stôp najmodernejšie nástroje a techniky. Optimálne kvalitatívne hodnoty zvuku totiž treba transformovať na digitálne dáta, s ktorými možno ďalej pracovať. Slúži na to unikátna „binaurálna hlava“, schopná digitalizovať fyzikálne parametre psychoakustickej kvality. Hluk sa zasa meria v špeciálnej bezdozvukovej komore, kde vzniká jeho digitálna akustická mapa, ktorá je základom pre optimálnu konštrukciu spotrebičov.
„Hluk a vibrácie sú dnes dôležitým kritériom, ktoré môže stopnúť sériovú výrobu niektorého z produktov“
Blízko Michaloviec
Z výsledkov zvukového dizajnu sa odvodia parametre, ktoré by mal sledovať inžiniering každého produktu. „Čím skôr sme do vývojového procesu zapojení, tým lepšie dokážeme eliminovať detské konštrukčné chyby výrobkov, ktoré by mohli na konci priniesť hlukové problémy. Samozrejme, je to aj nákladovo výhodnejšie, ako keď čosi riešime na poslednú chvíľu, čo obmedzuje naše možnosti využiť digitálne technológie“, tvrdí O. Petraška.
Modelovým príkladom je spolupráca s materským michalovským závodom BSH Drives and Pumps, ktorý ročne vyprodukuje do štrnásť miliónov elektromotorov pre všetky spotrebiče vyrábané v BSH pod hlavnými značkami Bosch a Siemens. Okrem silnej výroby sa na východe Slovenska rozvinula aj významná výskumná základňa BSH. V Michalovciach vzniká dizajn všetkých koncernových elektromotorov, pričom ide o desiatky rôznych typov v rozličných modifikáciách. Na druhej strane Košičania strážia ich akustické a vibračné parametre.
Digitálny vývoj
Košickí výskumníci vstupujú do vývoja motorov hneď v počiatočných fázach. V Michalovciach navrhnú tzv. rez motora, teda jeho elektromagnetický dizajn, konštrukciu rotora a statora. Návrh vzniká v digitálnom prostredí, čo umožňuje vytvoriť digitálny model motora a simulovať jeho činnosť, záťaže a overiť všetky výstupy – od fyzikálnych až po prevádzkové.
Košičania zároveň na digitálnom dvojčati sledujú zvukové a vibračné parametre návrhu. V softvéri LMS Virtual.Lab vytvárajú simulácie a digitálny model podrobia vibračným i akustickým analýzam. Zhodnotia vlastnosti motora a identifikujú zdroje jednotlivých zložiek hluku i vibrácií. Ak je to potrebné, navrhnú zlepšenia týchto parametrov, samozrejme bez nepriaznivého vplyvu na funkčnosť a cenu. Reálny účinok zmien potom digitálne overia experimentálne pomocou softvéru Simcenter Testlab.
„Môžeme zasiahnuť v každom štádiu simulačného reťazca a spätne povedať, ako sa zmena prejaví v základnom návrhu. Ak ide o štruktúru motora, rezonuje napríklad nejaká jeho časť, technickú nápravu vieme urobiť u nás. No ak problém vychádza zo samotného elektromagnetického dizajnu, treba sa vrátiť do Michaloviec a optimalizovať základný návrh. Takých slučiek zažijeme pri vývoji nového motora niekoľko“, hovorí O. Petraška.
Paralelne s vývojom Košičania pracujú aj na metodike merania zvukov a vibrácií motora po spustení jeho sériovej výroby. Na konci produkčnej linky sa každý finálny motor spustí na požadované otáčky, lasery bezkontaktne zosnímajú jeho charakteristiky a výsledky automaticky vyhodnotí softvér. „Celý proces merania nesmie trvať viac ako niekoľko sekúnd, aby sme neohrozili takt linky. Našim cieľom je tento čas ďalej znižovať zefektívnením niektorých procesov. Samozrejme za podmienky, že nestratíme kvalitu merania, ale naopak získame ešte lepšiu schopnosť zachytiť prípadné chyby“, vysvetľuje O. Petraška.
Virtuálny svet
Skupina akustikov začala digitálne nástroje využívať v roku 2008. Bola to cesta neznámou krajinou a museli prekonať viacero začiatočníckych prekážok. „Dnes je ale výsledok hmatateľný. Oba softvéry – Virtual.Lab i Testlab – sú od spoločnosti Siemens, čo nám poskytuje plnú kompatibilitu dát. Umožňuje nám to silne prepájať simulácie s experimentálnymi testami, ktoré sú veľmi dôležité, pretože bez nich by boli simulácie len pekné farebné obrázky“, hovorí O. Petraška.
Experimentmi overujú, či má simulácia správne nastavené parametre a poskytuje hodnoverné výsledky. Využívajú ich aj na odladenie všetkých možných variantov a úprav. „Ak napokon simulácia ukáže optimálny výsledok, ide sa do výroby reálneho prototypu. To je ďalší dôležitý prvok, ktorý má pozitívny vplyv na náklady – fyzický prototyp staviame až vtedy, keď sme si istí, že sme dosiahli najlepší možný výsledok“, vysvetľuje O. Petraška.
Vo virtuálnom svete sa všetko zrýchľuje a vývojové časy sa aj vďaka pokroku hardvéru neustále skracujú. Čo predtým trvalo týždne, zvládnu teraz za pár dní, niektoré časovo náročné simulácie skrátili z dní na hodiny. V budúcich rokoch by chceli ďalej zdokonaľovať simulácie, aby vyžadovali menej experimentálnych testov.
Exaktnejšie definované podmienky pritom neumožnia len presnejšie simulácie. Dovolia tiež lepšie predvídať, ako sa budú produkty správať v dlhodobej prevádzke. „Zákazníkovi chceme garantovať, že náš výrobok si aj po rokoch prevádzky zachová rovnaké hlukové a vibračné parametre ako keď si ho kupoval. Potom bude značke veriť a kúpi si aj ďalšiu generáciu našich spotrebičov“, uzatvára O. Petraška.
Softvéry pre digitálnu konštrukciu
Softvér LMS Virtual.Lab je digitálny nástroj na simuláciu a optimalizáciu výkonnosti mechanických systémov v oblasti konštrukcie, hluku a vibrácií, v dynamike a spoľahlivosti systému. Umožňuje presne simulovať funkčnosť a správanie sa mechanického návrhu, rýchle posúdiť viaceré navrhované alternatívy, zistiť ich slabé miesta a optimalizovať tak návrhy pred konštrukciou prototypu.
Riešenie Simcenter Testlab pre inžinierske testovanie kombinuje vysokorýchlostný zber dát s kompletným súborom analytických a modelovacích nástrojov pre širokú škálu testov. Poskytuje výhodný pomer medzi jednoduchosťou použitia a technickou flexibilitou a umožňuje zároveň overiť výsledky v simuláciách. Prináša tak spoľahlivé výsledky v konštrukčných tímoch, ktoré majú obmedzené možnosti stavby prototypov.
V záverečnej piatej časti seriálu si prečítate, čo všetko môže digitalizácia zlepšiť aj vo vašej firme.
Odborná spolupráca
